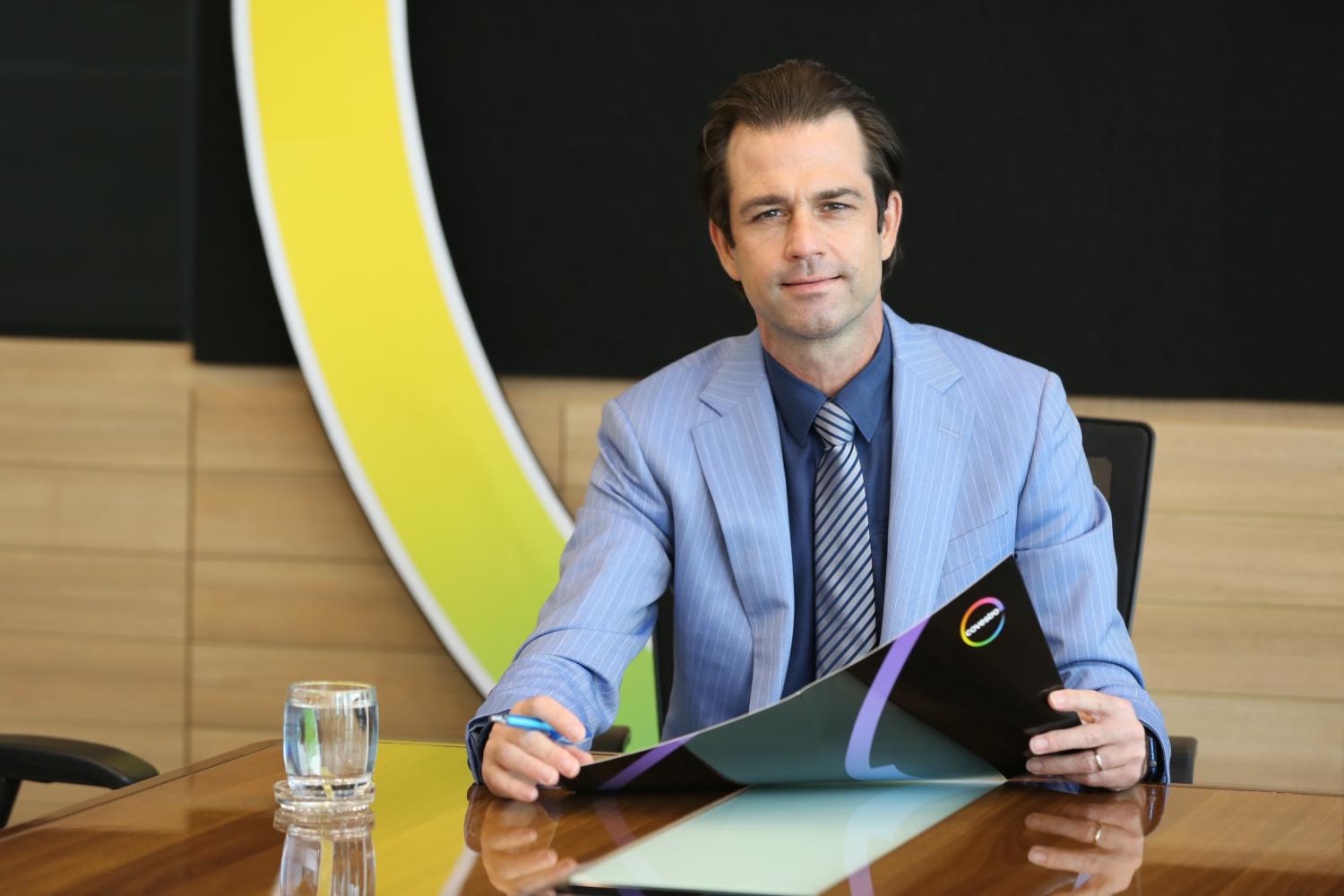
The global climate movement has grown exponentially, demanding that world leaders and governments walk the talk on environmental and societal issues to keep the rise in global temperature below 1.5C above pre-industrial levels.
Companies, particularly those related to the fossil fuel industry, are at the centre of the conversation as the industry accounts for 89% of global carbon dioxide emissions, according to a 2018 report by the Intergovernmental Panel on Climate Change (IPCC).
The plastic industry is deeply implicated as most plastics are made from oil. However, with growing demand from consumers and environmentally conscious customers, companies are exploring new ways to sustainably produce plastics and applying the circular economy concept to their business model.
"I think, for us, as a species being in this wonderful world, it's our duty to make sure that we hand over to the next generation a chance to also enjoy it," says Dr Timo Slawinski, managing director of the Thai unit of Covestro, a leading global manufacturer of high-tech polymer materials.
"I personally believe that there will be a lot of more pressure from society," he says, adding that companies that do not follow the new social norm will eventually drop out of the game and be replaced by others.
"This is why Covestro decided to be a frontrunner, not a follower," he says. "We want to be a pioneer because it makes sense. By being fully circular, it fits our vision and purpose to make the world a brighter place for the next generation."
CIRCULAR MODEL
To be fully circular, the company has committed to the Sustainable Development Goals (SDGs) of the United Nations and to its own goals. Covestro has also set non-financial targets to reduce specific CO2 emissions by 50% in 2025.
Specific reductions mean producing the same amount of product but emitting only half of the CO2 used in the manufacturing process, Dr Slawinski explains, adding that even a 50% reduction is "not enough".
The company also aligns its business growth with environmental goals by applying the principle of People, Planet, Profit (3Ps) to the decision-making process that guides research and investment. Using this principle means trying to optimise two factors without jeopardising another one, Dr Slawinski explains.
To be fully circular, customers play an important role as they are one actor in the value chain. Covestro works with clients in various industries including electrical appliances such as printer and mobile phone companies, furniture, automotive, transport and construction.
Covestro is starting to see increasing demand and willingness to pay a premium from high-end customers who want to use recycled materials to reduce their carbon footprint, says Dr Slawinski, adding the company is working with clients that want to shift their production as well.
He believes that by introducing better technology and convincing as many customers as possible, combined with pressure from society on all suppliers to be environmentally friendly, more companies will shift toward alternative materials.
Government efforts such as rising the CO2 tax and increasing energy and fossil feedstock prices will accelerate the shift, making alternative materials more attractive, says Dr Slawinski.
INNOVATION
Covestro has continuously developed innovations to use in the plastic manufacturing process to meet its circular goals. One of its groundbreaking solutions involves directly using CO2 as a feedstock, instead of using crude oil.
The company is now able to manufacture products made up of 20% CO2. The resulting foam material is now used in mattresses and sports floors, as well as in the automotive industry for vehicle interior sittings such as door panels, armrests and car seat linings.
The company also tries to close the loop where is possible. It is working with its partners and customers to bring back waste mattresses by reusing components such as foam and steel as feedstock for new mattress.
Another solution involves using biomass and vegetable oils and transforming them into feedstock. The proportion of carbon content can be up to 50% in the new material, further reducing the CO2 footprint in the manufacturing process.
A mass-balance approach is used in the latter process to ensure the use of recycled content in the final products. This prevents companies from "greenwashing" a product as "recycled" when it contains little to zero recycled material.
Not only plastic manufacturers but also feedstock suppliers need to be certified by an independent body, International Sustainability and Carbon Certification (ISCC). Covestro's plants in Europe and China have received ISCC Plus certification.
At the company's Thailand plant in Map Ta Phut, "we're putting a lot of effort into getting it very soon," Dr Slawinski says.
INTO THE FUTURE
Even though Covestro produces high-tech plastic materials, Dr Slawinski admits "we have a plastic waste issue" as single-use plastics have become a global problem. Research published in the journal Nature Climate Change has said that if production continues at the current rate, single-use plastics could account for 5-10% of global greenhouse gas emissions by 2050.
"We are suffering a lot in terms of reputation. … That is also a threat for the business, obviously," says Dr Slawinski. "This is why we are engaging in a lot of initiatives to convince society and governments that plastic waste should be recycled."
At its Map Ta Phut site, the company encourages its staff and their families to collect waste, particularly PET bottles, from their households so that it can be recycled. It is also involved in community activities including cleaning up the beach and educating local children through storybooks about marine litter and the circular economy concept in a fun and engaging way.
At the national level, Covestro is a member of Thailand PPP Plastics, a public-private partnership working to tackle the waste issue and promote policies and infrastructure to properly manage waste.
On the global scale, Covestro has committed to Operation Clean Sweep, pledging to keep plastic pellets from entering the waterways and oceans. It joined the Alliance to End Plastic Waste (AEPW) in 2018.
Looking ahead, Covestro has announced a strategy that consists of three chapters, says Dr Slawinski. The first is to "become the best of who we are". The company will optimise the organisation in terms of cost structure in order to be able to invest more in sustainability.
Covestro plans to spend almost 1 billion euros over the next 10 years on circular economy-related projects, he adds. "We are currently working to make sure that we have enough resources, enough money and a good organisation to implement systems."
The second chapter is to drive sustainable growth. Given the technology that "is ready to be substituted" and the products that can help reduce CO2, Dr Slawinski acknowledges that the technology in some areas still needs time to develop, while existing technologies will need to be improved as well.
The two chapters lead to the final chapter which is to become fully circular. To achieve those goals, Covestro needs to work in collaborative ways with partners and customers throughout the value chain to create a closed loop.
"If we keep on running at the front and do the transformation, we have a bright future," he adds.